Concordia SAE AeroDesign
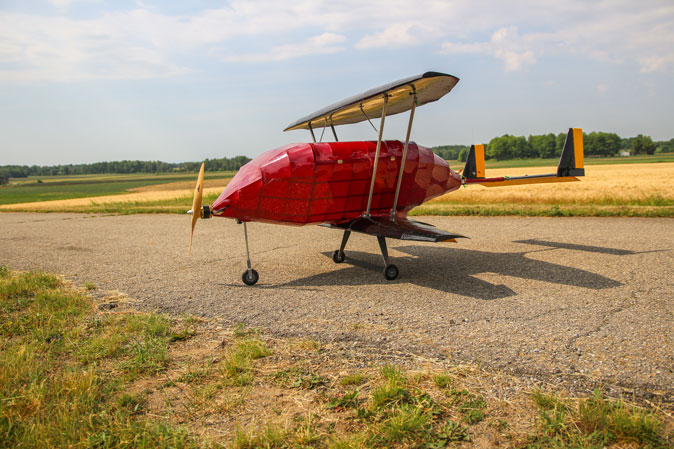
Concordia SAE AeroDesign is a team of 20+ members that spends most of their extracurricular time designing and making a large-scale RC Aircraft, with the aim of transporting very large amounts of cargo in the most efficient way possible. The team competes in SAE AeroDesign competitions, which are real‐world design challenges designed to compress a typical aircraft development program into one calendar year.
In 2021, Concordia SAE AeroDesign competed in the Regular Class of competition, as well as Advanced Class. The goal? Carry soccer balls as spherical cargo as well as steel plates, with a max take-off weight (MTOW) of 55lbs. Points were rewarded based on maximizing the count of spherical cargo and steel plates, while also minimizing cargo bay length and wingspan (which make it harder to maximize cargo and increase lift, respectively),
The goal for them was to build on and improve the design made the previous year. At the 2020 competition in Lakeland, Florida, the Regular Class team achieved 10th place overall.
“We no longer wanted to simply compete and achieve a high ranking; we were aiming to take the top spot through an ambitious design and a high score that was 2x higher than what the top team had managed to achieve the previous year,” says Tejas Iyer, AeroDesign structures lead and mechanical engineering student at Concordia. “Our goal was to think outside the box, explore new, unseen directions, and justify each decision.”
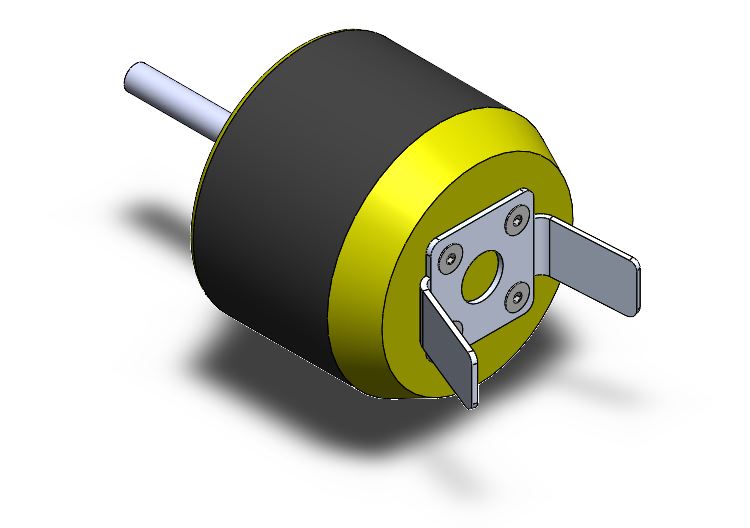
To do that, the team focused on improving the design process through preliminary and critical design review presentations. In addition, the team engaged with industry members, faculty and Concordia alumni who had previously been a part of the university’s SAE AeroDesign team.
For the team to reach its goal of finishing first place, and aiming for a score two times higher than the previous winner’s score, they knew they had to take risks in their design. “For us, this translates into an ambitious design, as some of the design choices were previously unseen in our society and had no precedent, which meant our design had an equal chance of failing as succeeding,” explains Tejas. The design included a biplane (an aircraft with 2 sets of wings) to achieve the lift requirements with a drastically reduced wingspan. In previous competitions, the team had focused on aircraft with only one set of wings. “Designing this involved increased work from the aerodynamic and structures sub-teams, and accounting for factors that we could not foresee at times.”
The team’s lofty goals and design also dictated that the layout for the spherical cargo (soccer balls) be arranged in a manner that produced the biggest aircraft fuselage that the society has ever seen. The aircraft’s main body would span 27” in width, compared to 9” in width in the previous year’s design. On paper, a design this big seemed to prove it could work on paper, but would it fare the same in a real-life flight test?
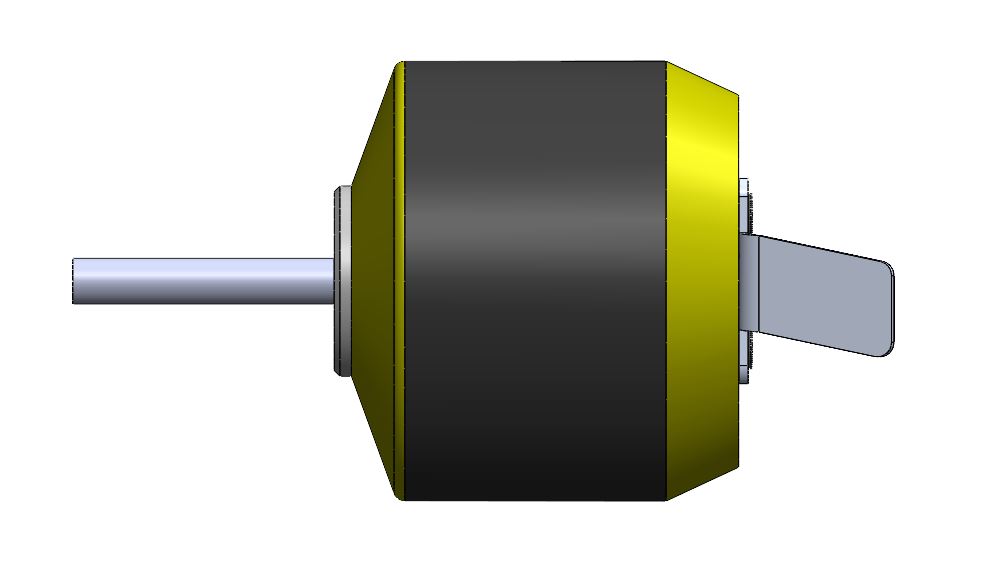
To get this design optimized, the team worked to minimize the weight of each aircraft component as much as possible, in order to maximize the weight for cargo while also remaining at the max take-off weight. That meant there needed to be even more simulations and analyses, as well as working in the unfamiliar territory of sheet metal. Enter Protocase!
The team took advantage of Protocase’s student sponsorship program by designing two unique parts. The first was an aluminum attachment piece that secured the electric motor to the rest of the fuselage through riveting.
The second component sourced through Protocase’s ultra-fast custom manufacturing was a built-up beam made of aluminum sheet metal. “When assembled, these beams produced the main structural component of our top wing in the biplane arrangement, which also provided support against lift as well as torsional forces,” says Tejas.
Working with many different sponsors, the team got real-life experience working with fabricators and vendors. When it came to working with Protocase specifically, the team enjoyed the professionalism, transparency and organization.
“One of the aspects we appreciated was the E-Drawing approval process. It gave us a clear idea on the status updates of the parts to be manufactured, and provided a simple platform on which revisions could be made without creating confusion,” says Tejas.
Both the aluminum attachment piece and bent-up beam designs that were submitted to Protocase for manufacturing didn’t have to undergo a lengthy back-and-forth process of redesigns.
“What we learned, and we find that is of more importance to us, is the process by which companies such as Protocase work. On a technical level, we now know what kind of capabilities these companies have in terms of design and manufacturing, which will save us time in our next design by doing it right the first time. On an administrative level, we also seek to work with companies that have the same organizational proficiency as Protocase, question to save time in the supply chain process and have confidence in our manufactured parts.”
In the end, Concordia SAE AeroDesign could not attend the SAE AeroDesign competition due to COVID-19 travel restrictions. However, the team put its design through its paces by competing remotely in Saint-Remi, Quebec. “
The Regular class team encountered technical difficulties during the first flight round, however, that did not prevent the team from fixing them and flying a second round. The Advanced class team flew admirably from the start, and did not look back.”
With all of this design experience, time testing and iterating the design, Tejas considers it a successful year for Concordia SAE AeroDesign. Going forward, he and the team are focused on ensuring all of the valuable knowledge gained can be transferred to incoming students to the team.
“Design is an endless, iterative process that only ends when one stops seeking improvement.”