The Formula SAE Electric (Society of Automotive Engineers) competition is an engineering design event for undergraduate and graduate students that first began in 2013. Competing students are tasked with developing and constructing a single-seat, fully electric powered race car to partake in both static and dynamic events. This provides participants with a chance to further improve their skills in engineering, design, and project management, as well as get some hands on designing experience.
In the competition, each group of students is a design team for a fictional manufacturing company that has contracted them to develop a small Formula-style car, and the prototypes that they design will be evaluated as a potential production item. The teams then design and build their prototypes based off of a set of rules promoting critical thinking to solve certain problems. Once teams arrive at the competition, experts in fields such as motorsports, automotive and aerospace observe the builds and assign scores based off of factors such as the car's fuel efficiency, acceleration, presentation, overall design, total build cost, and their capabilities in dynamic racing activities.
Illini Formula Electric (IFE)
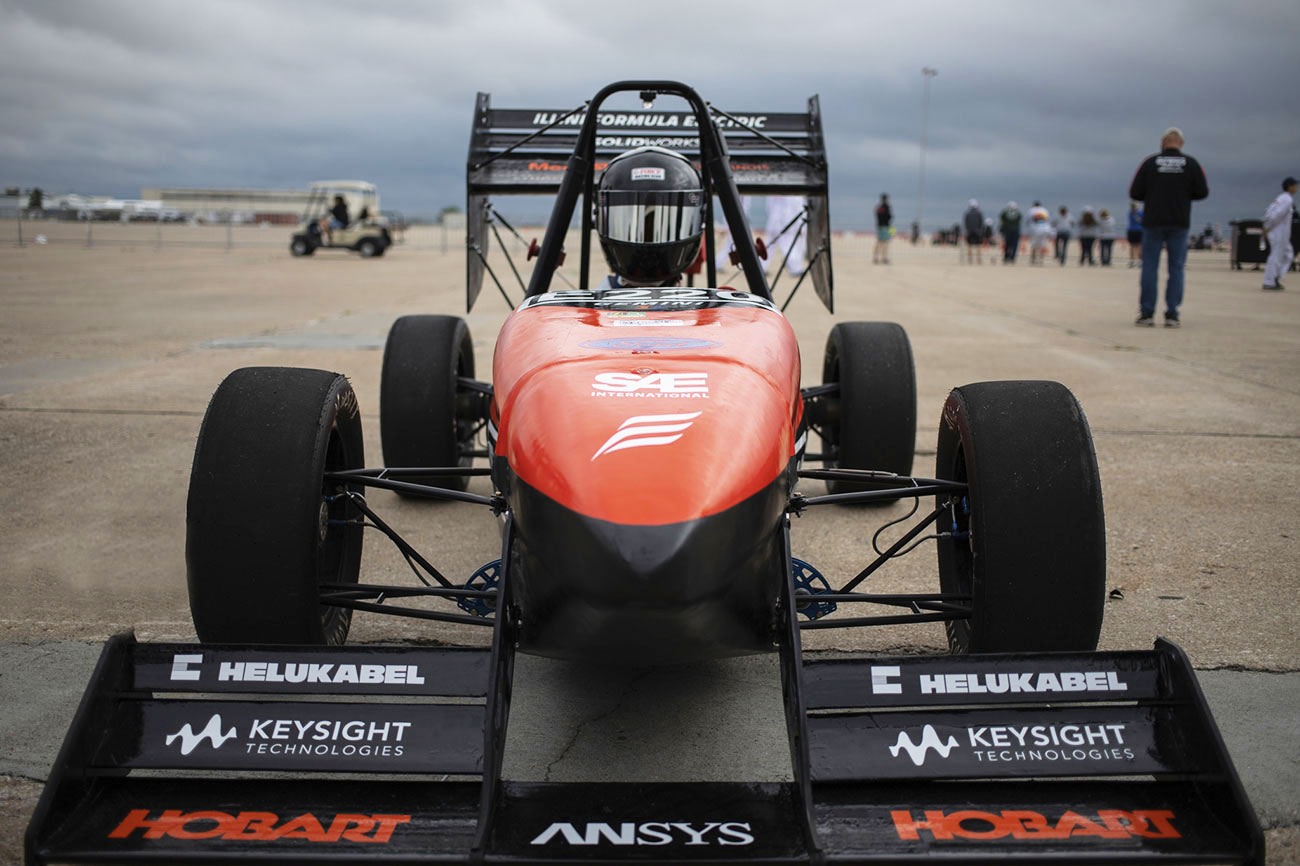
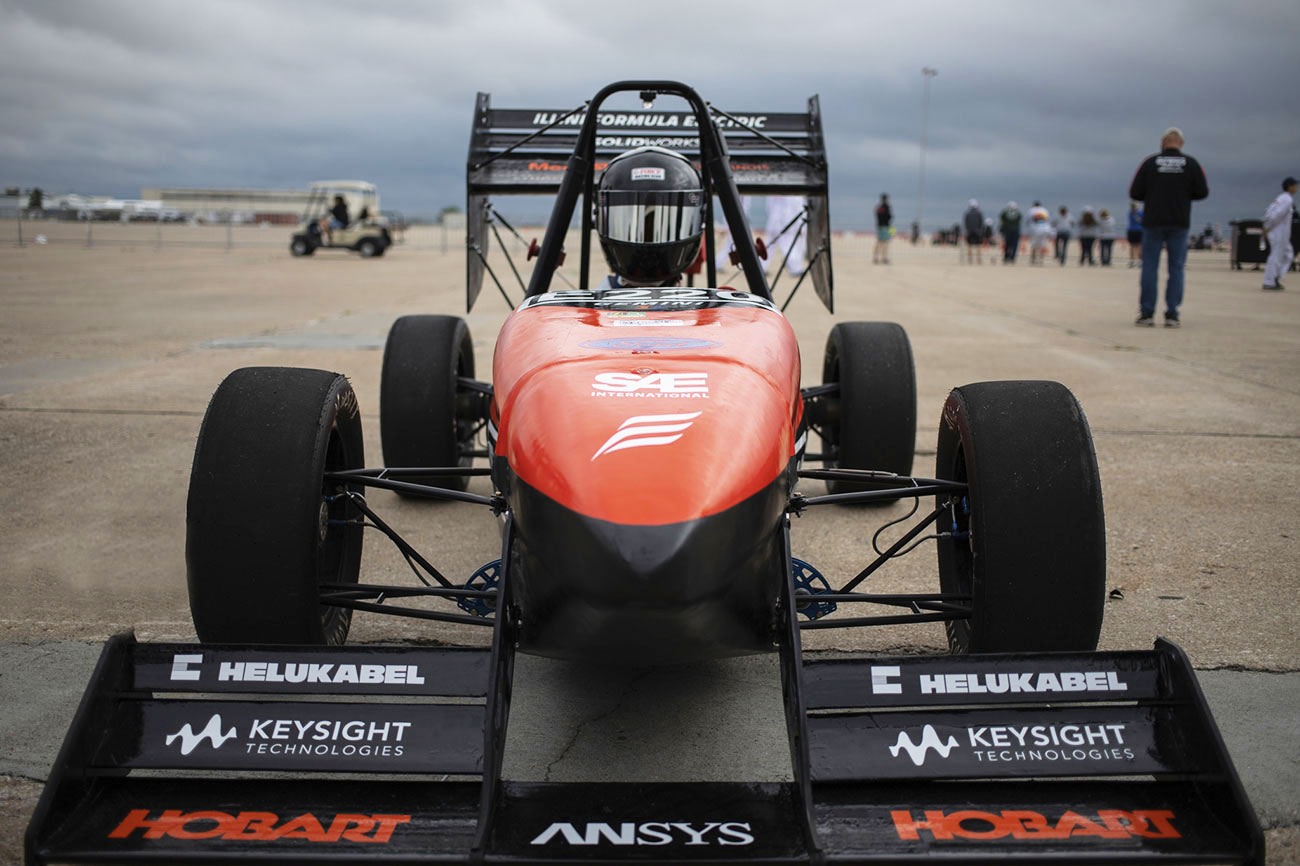
This year, the Formula SAE competition took place in Nebraska, where the University of Illinois' team, Illini Formula Electric, was looking to have another successful showing. Daniel Rhyoo, the manufacturing captain of Illini Formula Electric, says that one of their main goals for this year was to improve the aesthetic and manufacturing finish of their car from the previous year. The team also wanted to make changes to the size of their vehicle, to make it both lighter and more compact.
The team chose to work with Protocase to build a new accumulator case, which is essentially the car's area of energy storage where the main battery powering most of the machine can be found. This case needed to fit snugly into a confined space, meaning size tolerances were of the utmost importance.
The accumulator case had to be able to withstand a 40g force in the XY plane, 20g force in the vertical axis, and 20kN on all the mounting points.
"We had Protocase manufacture the outer walls of the box from a single bent sheet metal plate," explains Rhyoo. "From there, we machined and welded the internal walls as well as the accumulator mounts. Protocase creating the outer walls of the case made the overall process of finishing the accumulator much easier."
With design, weight, and tolerances all playing a key role to the overall success of the car, the team had high expectations for the accumulator case that Protocase would manufacture. "We expected a clean finished accumulator outer case and lid, but were worried about the tolerances due to its size and unusual geometry," says Rhyoo. "Upon arrival, we were very impressed with the finish of the final product and the tolerances it maintained."
Formula SAE Electric 2018
Formula SAE Electric 2018 was held in Lincoln, Nebraska in June. The team's design decision to focus more on improved quality of their components and reduced weight helped them achieve better scores in almost every category, placing them 5th overall in the design category.
"At the competition, we weighed in 45lbs lighter than last year, and made it through the electrical and mechanical inspection much faster than ever before," says Rhyoo. "We even had judges compliment our accumulator on its finish and quality, and greatly smoothed the inspection that normally was a great difficulty for us."
Illini Formula Electric's future plans
Next year's event will mark the biggest design change for their car. IFE plans on creating a brand-new car with a new battery composition and motor. Nothing on their car from this year will carry over, increasing the stakes for the team.
Despite this challenge, Rhyoo and his teammates are very optimistic. "This change will allow us to transition to a more efficient system without having to bandage previous year's flaws. One of the biggest impacts of this shift is a new battery composition, which will lead to a much more complex accumulator design that we hope we can work with Protocase again to create."