


CNC Milling
Bare Metal Finishes
CNC Machining creates a unique finish with visible toolmarks, due to the spinning motion produced by our CNC milling machines' cutters. Minor surface scratches, blemishes and swirl marks are to be expected for a CNC machined part with no additional finishing applied.
No Finish:
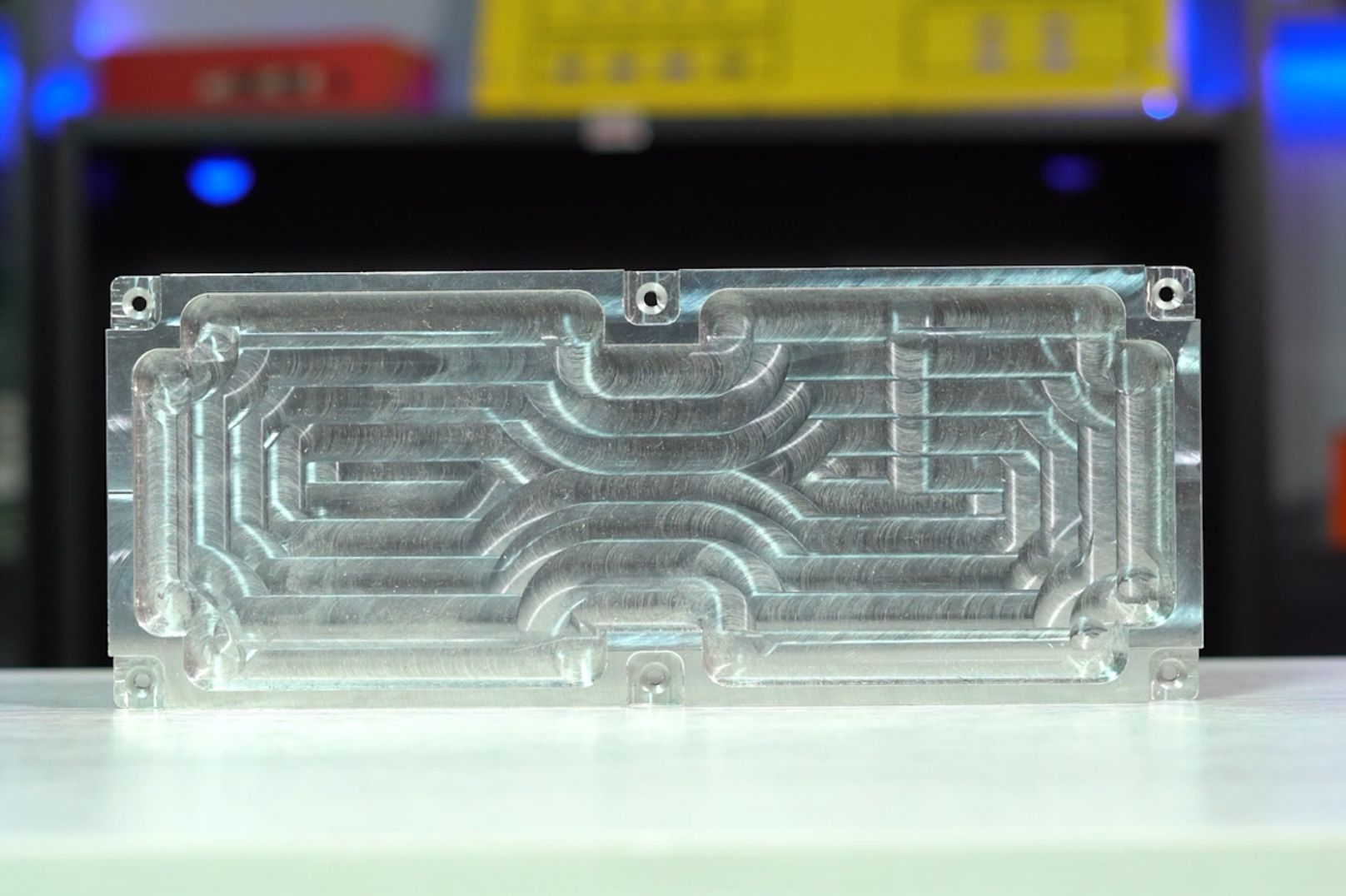
The as-is appearance after a part is machined. There will be visible toolmarks in swirl patterns, due to the spinning motion produced by the CNC mill's cutter.
Things to Consider:
- • Appearance is not decorative in any way. No Finish is best for parts that will not be on display.
- • Most cost-effective option where a uniform finish is not required.
Stock Finish:
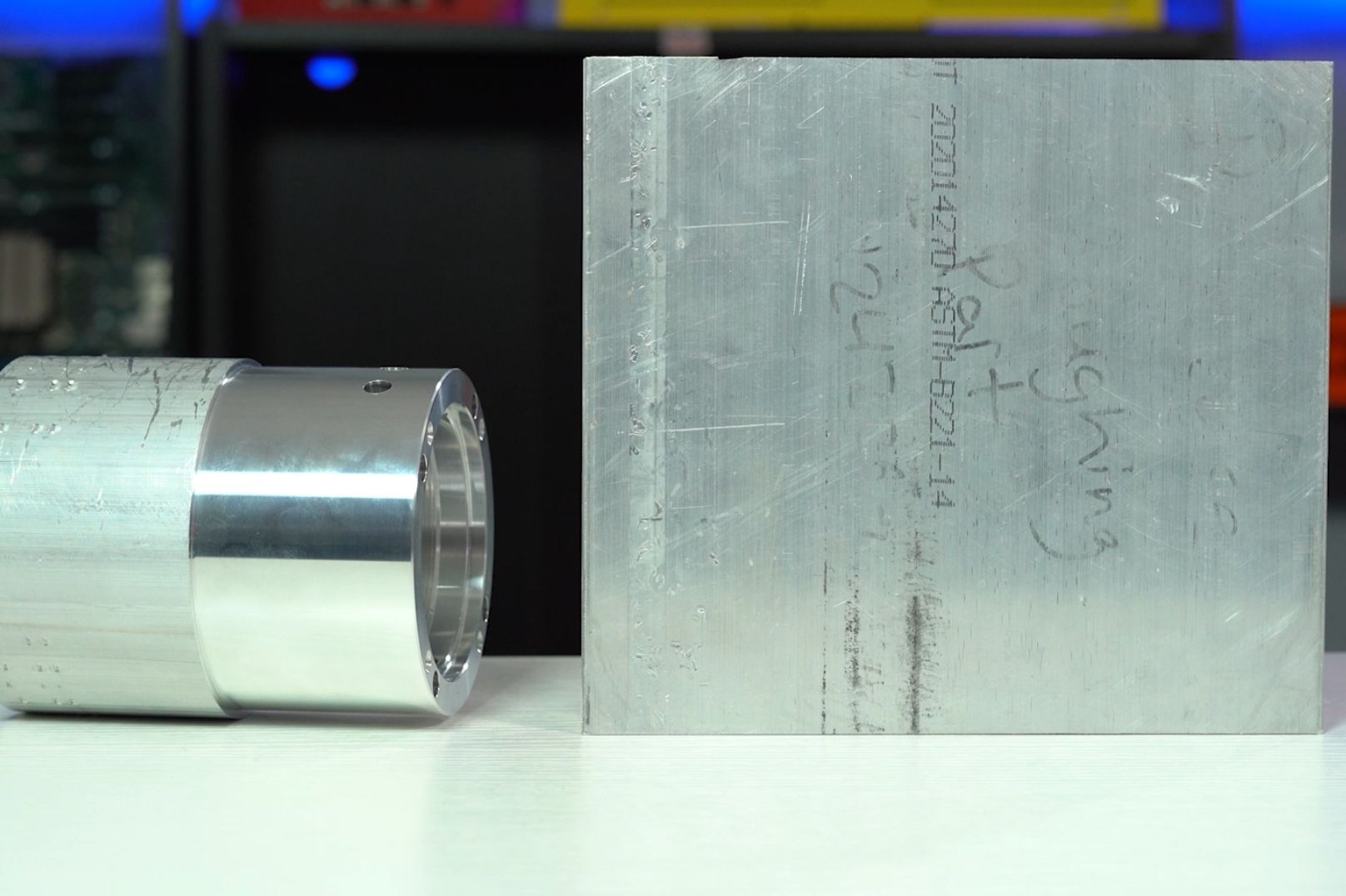
Stock Finish is similar to No Finish parts in that there is no additional finishing applied, except the outer surfaces of your machined part are the raw material that was milled (For example: 0.5” plate or square tubing). Stock Finish parts may have scratches, as well as material identification print or stickers from the supplier.
Things to Consider:
- • Appearance is not decorative in any way. Stock Finish should only be chosen if the parts will not be on display.
Learn more about Stock Finish.
Grained Finish:
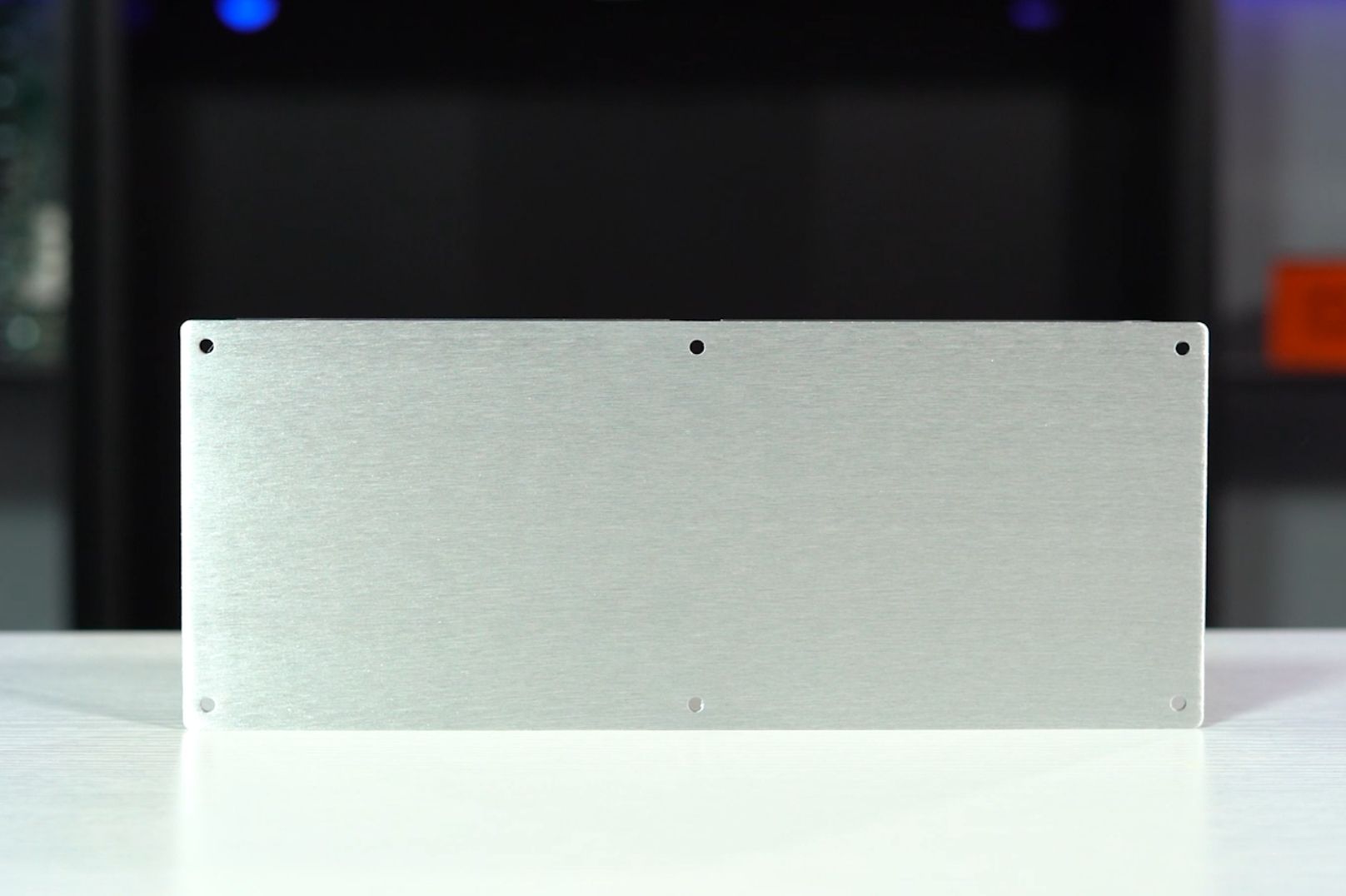
Once a part is CNC milled, the surface is finished using a brush/sander in order to achieve a specific grain.
Things to Consider:
- • Ideal for flat parts
- • Due to geometry, grained finish can only be applied to the outside surfaces of CNC machined cases and parts are not on the inside pockets.
- • If choosing grained finish for machined parts with pockets, only the outermost surfaces will be grained finish. The pockets will remain unfinished.
- • Parts with protruding features or bosses limit the ability to apply grained finish.
- • Can be digitally printed, silkscreened, laser marked or engraved (as long as it’s a flat surface)
Learn more about Grained Finish.
Media Blasting:
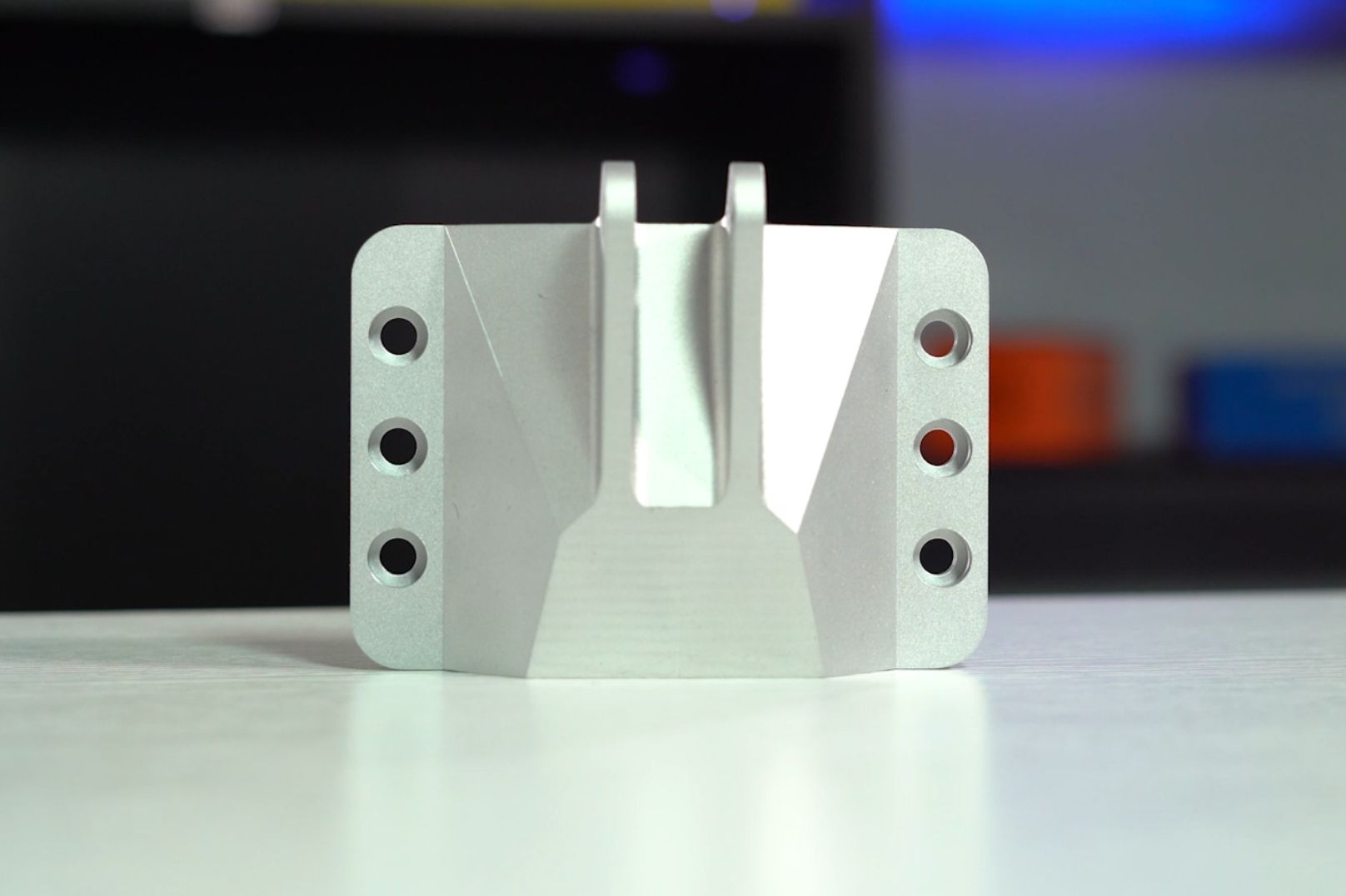
Once a part is CNC milled, the part is deburred and then a stream of tiny glass beads is sprayed onto the surface via compressed air. The end result is a bright, more uniform finish.
Things to Consider:
- • Excellent option for removing toolmarks from machined parts.
- • Flat, non-directional finish.
- • Maximum part size is 6”x6”x6” (152.4mm x 152.4mm x 152.4mm)
- • Parts must have a minimum of at least one dimension that exceeds 2”
- • Risk of warpage for thin parts and/or large surface area parts
- • Can be digitally printed, silkscreened, laser marked or engraved (as long as it’s a flat surface)
- • We recommend handling with gloves in order to avoid staining or smudging the parts
- • As media blasting is a manual process, results may vary in terms of uniformity, especially when anodizing will be applied to your media-blasted part
Learn more about Media Blasting.
Vibratory Finish:
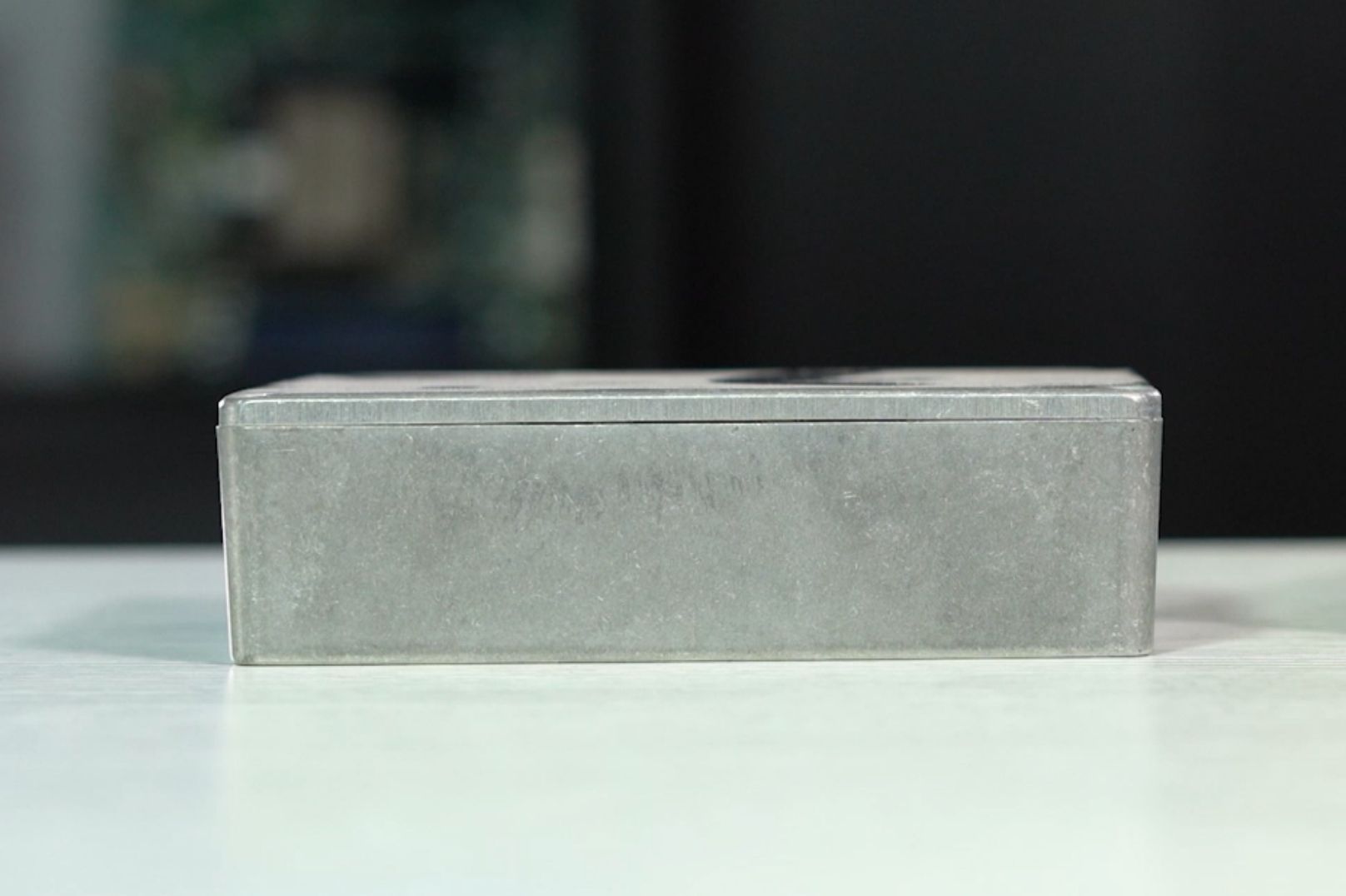
After milling, parts are processed via a vibratory tumbler in abrasive medium to impart a random (non-directional) matte appearance that is similar to frosted glass.
Things to Consider:
- • Limited to parts 10"L x 10"W x 10"H (254mm x 254mm x 254mm) or smaller
- • Ideal for smoothing over rough edges
- • Vibratory finishing will minimize the appearance of toolmarks, but not completely remove
- • Can be digitally printed, silkscreened, laser marked or engraved (as long as it’s a flat surface)